The RootMaster is a Raspberry Pi Zero 2W-based hydroponic automation system designed to precisely manage water and environmental conditions. The solution also integrates an STM32G4 microcontroller to handle real-time operations such as controlling pumps and peripherals, managing sensors, and processing data from external sensors like water level indicators. It also generates PWM signals to control the power of connected devices and handles communication with external modules through a CAN FD interface.
While STM32 handles hardware-level tasks, the Raspberry Pi Zero 2W manages high-level control and user interaction. The RootMaster can be programmed with Python, C, C++, or other programming languages and is useful for applications like Hydroponics automation, water circulation, and environmental control.
RootMaster specifications
- MCU – STMicro STM32G473 32-bit Arm Cortex-M4 microcontroller @ 170 MHz for real-time operations
- Main controller – Compatible with Raspberry Pi Zero 2 WH for GUI and other interfaces
- Sensors
- pH sensor for nutrient solution acidity monitoring
- Water temperature sensor to prevent root shock
- EC (electrical conductivity) sensor for tracking nutrient concentration
- Air temperature and humidity sensor for environmental monitoring
- Flow meter for water flow rate detection
- 3x digital inputs for additional sensors (e.g., water level indicators)
- Outputs:
- 6x high-side switch outputs for pumps and valves (0-12V, PWM control)
- Support for up to 3 pumps and 3 valves (peristaltic or water pumps)
- Expansion
- CAN bus interface supporting CAN FD up to 1 Mbit/s for system expansion
- 3x digital inputs
- Power
- 12V power from DC barrel jack
- 12V from USB-C PD
- Dimensions – 101.0 x 101.0 mm
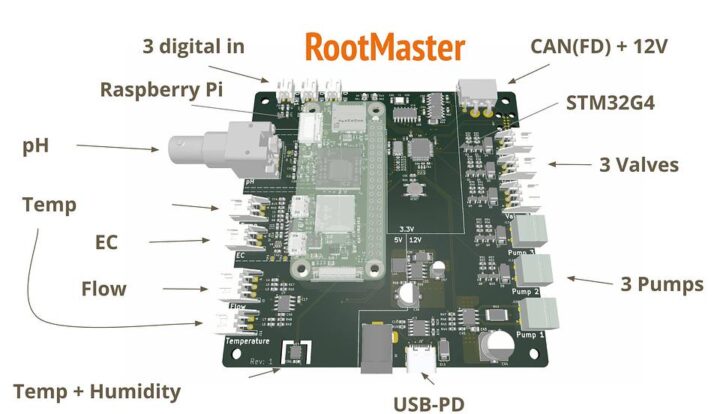
The hardware is open source so after looking at the schematics for a bit I can see that the HDC1080 digital temperature-humidity sensor is soldered on the board, and other sensors get connected to the board externally. Other than that there are TPS60400DBV negative voltage generator, ADS1115IDGS ADC, MCP4017T-502E/LT digital potentiometer, ADM3260ARSZ-RL7 isolator with Integrated DC/DC converter, REF3020 voltage reference, TLV271 Op-amp, CH224K USB PD controller, TPD2EUSB30 ESD protection diode, AMS1117-3.3 voltage regulator, TPS5430DDA buck converter SN65HVD230 CAN Transceiver, MCP2518FD-xQBB CAN FD controller, and AT24C256C EEPROM onboard.
In terms of programming the RootMaster supports multiple programming and debugging options for different developer needs, there is the TagConnect 10-pin (TC2050-IDC) interface, a 2.54″ pin header compatible with STM32 Blue Pill, an optional Cortex Debug connector for advanced debugging, and USB DFU for straightforward firmware updates. The hardware design files (KiCad schematics, PCB layout, etc,..), 3D files, Rust firmware, and ” Hydroponic Flower Control” web interface can be found on OpenHydropnics’ GitLab account, and some documentation is available on the OpenHydroponics website including the instructions to enable the CAN Bus and 1-wire interfaces on the Raspberry Pi OS.
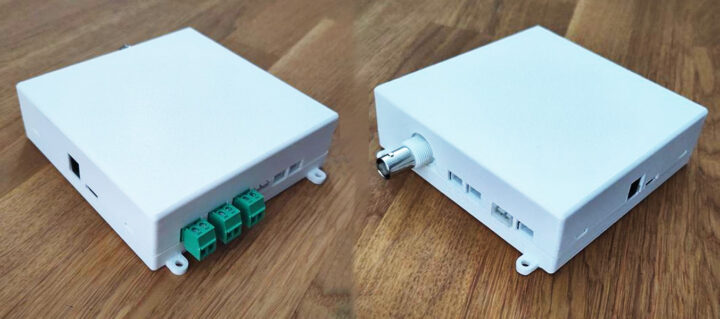
Previously we have written about agricultural products like the SenseLora 4G Gateway, the WisGate Soho Pro RAK7267, and Eduponics Mini v2.0 Smart Agriculture IoT kit. Feel free to check those out if you are interested in Smart Agriculture solutions.
The RootMaster Raspberry Pi-based hydroponic automation system is available on Lectronz and Tindie for about $54.00. You’ll also need some accessories to connect it to, and the developers tested a 12V power pump and a water conductivity and temperature sensor both available from AliExpress.

Debashis Das is a technical content writer and embedded engineer with over five years of experience in the industry. With expertise in Embedded C, PCB Design, and SEO optimization, he effectively blends difficult technical topics with clear communication
Support CNX Software! Donate via cryptocurrencies, become a Patron on Patreon, or purchase goods on Amazon or Aliexpress
I don’t feel like 170MHz Cortex-M4 is enough to process temperature and moisture sensors data and control pumps at the same time, it’s more likely a task for Intel Core i9, probably two.
yeah, good luck attempting any of that without AI
You might also want to take a look at https://github.com/hydromisc/hydromisc which serves a similar purpose but is ESP32-based.
Nice design but look this WIZCUBE.EU platform. It is introduced years ago and embraces Raspberry Pi bus plus Raspberry Pico on board .All in a 90x90mm PCB Zto easily fit into 200x200mm box.
All inputs and outputs are industrial grade 24v opto isolated. More boards to come
Open source Kicad created
Enjoy and build upon it