Here’s another ESP32 3D printer controller board with the Phi MainBoard 5LC powered by both an ESP32-S3-WROOM module and a Microchip SAME51 Cortex-M4F microcontroller, and providing Ethernet and WiFi connectivity.
Designed by Likha Labs from the Philippines, Phi MainBoard 5LC is pre-loaded with RepRapFirmware firmware running the Duet Web Control interface that allows users to upload G-code files, configure settings, start jobs, control the device, and monitor prints. Besides 3D printers, the developers explain the board can also be used to drive other digital-fabrication equipment, such as CNC machines.
Phi MainBoard 5LC 3D printer controller specifications:
- MCU
- Espressif Systems ESP32-S3 dual-core Xtensa LX7 WiFi and Bluetooth microcontroller @ 240 MHz with 512 KB SRAM, 8 MB SPI flash via ESP32-S3-WROOM-1-N8 module
- Microchip ATSAME51N19A Cortex-M4F microcontroller @ 120 MHz with 512 KB flash, 192KB SRAM
- Storage – MicroSD card socket
- Connectivity
- 10/100M Ethernet
- 802.11b/g/n 2.4 GHz Wi-Fi 4
- Bluetooth 5.0 LE
- USB – 1x Micro USB 2.0 port up to 12 Mbps
- Machine features
- 5x TMC2209 stepper drivers with up to 256x micro stepping
- 2x extruder heaters, each up to 5A
- 1x bed heater up to 15A
- 3x thermistors or PT1000s
- 4x PWM fans, 1x always-on
- 1x VFD/Laser/Servo (5V output)
- 7x GPIO ports with 30 V tolerant inputs, 3.3 V outputs for end stops, filament monitors, Z-probes, SSRs, etc…
- Specialty ports
- Power Supply
- Input voltage – 11V – 25V DC
- Input connector rated up to 25A
- On-board regulators – 1x 12V, 3A, 2x 5V, 3A, 2x 3.3V, 1A
- Dimensions – 123 x 100 mm, M4 mounting holes (4-layer PCB)
The ESP32-S3-WROOM module handles networking, USB communication SD card storage, and displays, while the Microchip SAM E51 microcontroller takes care of real-time tasks like kinematics, stepping, digital and analog I/Os. A Github repository has been readied for the project, but it’s currently empty. Likha Labs say they’ll eventually upload hardware design files and publish documentation there. While they do not highlight that ESP32-S3 comes with AI instructions, I wonder if they could eventually be put to good use to detect issues or defects during printing and alert the user.
Phi MainBoard 5LC has just launched on Crowd Supply with a funding $55,000 target. There’s a single reward at $149 for the controller board pre-flashed with the firmware, a MicroSD card with the content to get started, and a bag of crimps, terminals, and housings for Molex KK 254, JST VH, and screw connectors. Shipping is free to the US and $14 to the rest of the world, and backers should expect the controller to ship in July 2022 if everything goes according to plans.
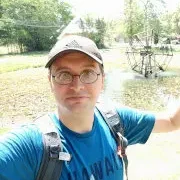
Jean-Luc started CNX Software in 2010 as a part-time endeavor, before quitting his job as a software engineering manager, and starting to write daily news, and reviews full time later in 2011.
Support CNX Software! Donate via cryptocurrencies, become a Patron on Patreon, or purchase goods on Amazon or Aliexpress
It looks as kind of strange design. Having ESP32-S3 just for WiFi connectivity does not make much sense etc. In my opinion RepRap firmware probably can be ported to ESP32-S3. Currently, the ESP32 ports of Marlin and GRBL does not seem to be quite optimized, the file upload speed is quite slow etc. Realtek’s RTL8722DM also seems quite appropriate for such solutions, but so far I am unable to find chips and modules.
Hi, creator of Phi here. It’s a partial port of RepRapFirmware to ESP32-S3, actually. RepRapFirmware has been split in half: the networking, storage, displays part of the code runs on the ESP32-S3; while the kinematics, stepper control, and other digital/analog I/O runs on the SAM E51.
In this case, ESP32-S3 acts more like an SBC rather than just a Wi-Fi module.
And what are the advantages of your solution in comparison to Duet 3 Mini 5+ (https://e3d-online.com/products/duet-3-mini-5) ? IMO for small boards having a secondary MCU is a waste of resources. By the way interesting what file transfer speed over Ethernet and WiFi you were able to achieve ?
Wi-Fi *and* Ethernet on a single board instead of choosing between the two, removing some shared signals, more and beefier on-board regulators.
I’m able to achieve peaks of 1MiB/s, average around 800KiB/s. Though there is still room for optimization.
Made some improvements. Peak is now 1.3 MiB/s, average is 1 MiB/s. There still some room for improvements…
With more and more people moving to Klipper, a board like this makes less and less sense. If this is your thing, then carry on, but even a RAMPS board and an Rpi running Klipper will perform better and have a better UI.
The maximum stepper rates of RRF on Duet Wifi boards (presume around the same speed with ATSAME5) were 240k / 130k, current version of Klipper with 20 MHz AVR – 196k / 123k. Not so sure about the Klipper issues with lost communication, timer too close etc. Klipper uses uart to communicate with microcontroller/s, which provides bottleneck for data transferring. There were issues in the past when Klipper used as laser engraver/cutter, latest tests were at 50mm/s, kind of slow etc.
Espressif products like ESP8266, ESP32 … are very unlikely to provide fast file transfer. Probably one of the reasons the latest Duet boards have a Linux port – 8 MHz SPI for connecting to a SBC like Raspberry PI.
The latest versions of Duet Web Control are not so good, personally I use v1. It doesn’t have some of the Repetier Server functionalities, still I find it convenient to work with. Which is your preferred UI ?
In regards to print quality, I had better results with Marlin and Repetier firmware. Somehow with RRF different issues appear. From RRF 3.4.0 beta 3 the motion calculations are done using floating point math, presume the print quality is improving.
So they move a connector or two around on a duet 3 mini board and call it their own and apply for funding? At least the Chinese give credit for their clones.
Ah, basing the board on the Mini 5+ is biting me in the ***. I did this because currently, I am the single person working on this and was hoping to base it on something users are familiar so that providing support becomes easier.
There’s nothing I can say except that it’s not a simple ‘moving a connector or two’ – there’s actually a lot of difference under the hood both in hardware and firmware.
Regarding the credits, I was actually planning to abide by Duet3D’s open-source license: https://github.com/Duet3D/Duet3-Mini5plus/blob/main/LICENSE. That is, in the final hardware revision, the packaging and PCB silkscreen will contain the required text for proper attribution.