Announced in 2019, NORVI IIOT industrial controller features an ESP32 WiFi and Bluetooth module, a choice of OLED or TFT Display, 24V DC input, and several analog and digital I/Os all housed in a DIN Rail enclosure.
Sri Lanka-based ICONIC DEVICES has now announced an updated version with NORVI ENET DIN-Rail ESP32 industrial gateway based on a similar design, but with the addition of an Ethernet port using W5500 SPI to Ethernet controller.
NORVI ENET (AE06) specifications:
- Wireless Module – ESP32-WROOM32 with ESP32 dual-core processor @ 160 MHz, 520 Kbytes SRAM / 4 Mbit Flash, WiFi 802.11 b/g/n, Bluetooth 4.2
- Storage – MicroSD card slot
- Display – Built-in 0.96″ OLED display
- Communication – 10/100M Ethernet via W5500 controller, WiFi, Bluetooth, optional LoRa or NB-IoT module
- I/Os
- 8x 24V digital inputs for rotary encoders, sensors
- AE06-R model only – 4x 5A relay outputs for solenoid valves, contactors
- AE06-T model only – 4x open collector high-speed transistors (PWM or PULSE outputs)
- AE06-V model only – 4x 0 to 10V analog inputs
- AE06-I model only – 4x 2-20mA analog inputs
- Misc
- Power, status, and I/O LEDs
- DS3231 RTC with battery backup
- Optional MAX31856 temperature sensor
- Power Supply – 24V DC rated input via terminal block
- Power Consumption – 32.6 to 40.4 Watts with all outputs ON
- Dimensions – 90.50 x 56.60 x 60.60 mm (DIN-Rail mount)
- Weight – Around 430 grams
- Mounting
- Top hat type TH35-15 rail conforming to IEC 60715
- Top hat type TH35-7.5 rail conforming to IEC 60715
- Plate or panel with fixing kit
- Compliance – 2014/30/EU- Electromagnetic Compatibility (EMC)
Annex III, Part B, Module C
There’s limited information about software support on the product page. But since it’s just an evolution of NORVI IIoT (even the dimensions are the same), with Ethernet replacing RS-485, NORVI ENET should be programmable with the Arduino IDE as the company provides Arduino libraries and sample sketches for inputs, outputs, RTC, temperature sensor, and the I2C display.
NORVI ENET ESP32 DIN-Rail industrial controller can be purchased through the aforelinked product page between $108 and $134 depending on the selected model.
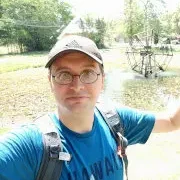
Jean-Luc started CNX Software in 2010 as a part-time endeavor, before quitting his job as a software engineering manager, and starting to write daily news, and reviews full time later in 2011.
Support CNX Software! Donate via cryptocurrencies, become a Patron on Patreon, or purchase goods on Amazon or Aliexpress
Weird decision, using a W5500 instead of the ESP32’s integrated Ethernet MAC.
This may be beneficial when using only the Arduino SDK, because the W5500 is well supported there, but absolutely nonsense if you plan to use the ESP-SDK and it’s integrated IP stack.
Also, using an ESP32-WROOM (without PSRAM) instead of an ESP32-WROOVER (with PSRAM) makes it hard to use Micropython.
And generally: When I already have a big DIN-rail hausing with mains power supply and Ethernet socket, I’d rather use something like a Raspberry Pi or similar. Doesn’t make much of a difference price-wise.
True, and i would guess most company’s developing for industies won’t use arduino, i would think c or c++
Actually, ladder logic (IEC61131) is still the most common, although it might depend on the sub-market (e.g. automotive, building automation, semiconductor, etc).
The Siemens Logo! is an example of a popular PLC for building automation; it uses graphical programming similar in approach to ladder logic, and is now available with wired Ethernet. (If you want to compare, the Siemens S1200 is an example of a factory oriented PLC).
Does the logo still exist?, i used it 20y ago when i was at school, it was indeed simple and usefull, you could even program it with 4 arrows and ok and cancel.
Yes; see the link below to Automation24 for Logo! and S1200 online pricing.
I started using the early models (I think we started with first generation) back around 2002 because our parent company picked it to manage switches and power logic in our machine. A few years ago, I designed it out since by then we had added a main PLC (Panasonic FP series) that could handle those functions, too.
I like the programming environment (Logo! SoftComfort) – it’s well suited for its task, and has always come with a simulator. SoftComfort was written in Java from the start, and I believe in the last few years Siemens has explicitly been supporting non-Windows OS’s.
The frustrating part was the lack of any monitoring communications, so troubleshooting could be difficult although using the screen you can check on the Inputs, Outputs, and IIRC, the internal blocks. I never used the on-machine programming, except maybe a few times to change some delays. The Ethernet models should be a nice upgrade.
https://www.automation24.com/control-systems
Very much related question… I am looking for a reliable wired ethernet reachable home automation system for our holiday home. Reliable, so:
I also want the solution to be as FOSS as possible.
So far, I’ve found:
Home Assistant with esphome
Esphome is almost always wireless, right? And I want this to just keep running if my Home Assistant doesn’t feel like running anymore…
Everything can be wired: https://esphome.io/components/ethernet.html
And with esphome you can do all kinds of device automation (without home assistant or mqtt) directly on a esp.