If you have a small production run for your board, it may not be cost-effective to ask a factory to manufacture it for you, and assembling the boards entirely by hand will be a time-consuming process. Getting a pick-and-place machine to automate the process would save time, but even the cheaper models on Aliexpress cost several thousand dollars.
Citrus CNC tries to address the cost issue with the SimplePnP open source hardware pick-and-place machine that brings the price down to several hundred dollars.
SimplePnP key features and specifications:
- MCU – Microchip Atmega328p running GRBL firmware
- Motor Drivers – TMC2209 stepper for two-phase stepper motors
- Word Area – 300 mm (X) x 300 mm (Y)
- Z Travel – 23 mm
- Components per Hour – 750 with vision assist
- Component Size – As small as 0402 (1005 metric)
- Vacuum Heads – Single vacuum head (base model), or optional dual-head
- Nozzle System – Juki 5xx with tool changer capable holder
- Vision – Top-vision and optional bottom-vision
- USB Camera Specs – 1280×720 @ 30 fps ( OmniVision OV9712 based)
- Host Interface – 3x USB ports
- Power Supply – 12V/5A (60 W)
- Dimensions – 500 × 450 × 200 mm
- Weight: 4 kg
As the comparison table above, SimplePnP is not the first open source hardware pick-and-placer around, but offer a much cheaper option compared to LitePlacer. The latter does provide a fairly larger work area however.
You’ll find the design files, hardware & software user manuals, and a PDF assembly guide on Github. You can also read the instructions to configure OpenPnP control software working on Mac OS, Windows and Linux.
Citrus CNC launched SimplePnP pick-and-place machine on Crowd Supply and already surpassed their $6,500 goal. Rewards start at $630 for the model with one nozzle holder, a top-vision camera, one rotation motor, one linear rail, a vacuum pump, a power supply, motion control electronics, and three vacuum nozzles. The price goes up to $920 for the dual-head model with two cameras and up to 12 vacuum nozzles. Shipping is free to the US, and $84 to the rest of the world. Backers should expect their rewards to ship at the end of May if there aren’t any delays with the project.
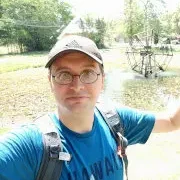
Jean-Luc started CNX Software in 2010 as a part-time endeavor, before quitting his job as a software engineering manager, and starting to write daily news, and reviews full time later in 2011.
Support CNX Software! Donate via cryptocurrencies, become a Patron on Patreon, or purchase goods on Amazon or Aliexpress
Nice, but what I would prefer would be to see just a pick-and-place module to use as a replacement for the head of a laser or CNC engraver. Because by having both the engraver and the simplepnp, you use twice the space on your desk and need to connect twice the ports. This way I could engrave, then place, all on the same table.
I get what you are suggesting, but it is not always a “best of both worlds” kind of scenario.
A 3D printer or engraver usually has the head constrained to stay above the print/engraving surface. I suspect that makes it difficult for the PnP head to reach parts trays, or position the part above the camera to allow for rotation/alignment recognition, etc.
And this is just the very first problem that comes to mind!
An engraver would probably end up throwing debris onto the upward looking camera, for example, or into the parts trays.
> A 3D printer or engraver usually has the head constrained to stay above the print/engraving surface. I suspect that makes it difficult for the PnP head to reach parts trays, or position the part above the camera to allow for rotation/alignment recognition, etc
I don’t get what you mean, there’s a working area that’s included into a rectangle, just like for this one. The spare parts just have to be placed anywhere out of the PCB provided that it’s reachable by the head.
> An engraver would probably end up throwing debris onto the upward looking camera, for example, or into the parts trays.
No, because when the engraving head is mounted, then the PnP one isn’t. It’s either one or the other.
I think the main difficulties would come from software support in fact, if you have to control the camera and adapt to the engraver’s firmware. But I’m seeing this PnP uses GRBL, just like my engraver, and quite a number of GCODE software support GRBL which makes me think it’s one of the few de-facto standards for this target audience. So probably that it wouldn’t require much adaptations to mount this head on an existing engraver.
Well, maybe that could come as an option later for those already having everything but the head, we’ll see.
Sure, I guess you could place the parts on the bed, around the PCB, and go like that. I suspect that the parts would end up being shuffled around if the bed is moving, though. Ideally you would want something like a CoreXY configuration with a bed that moves only in Z, if you wanted to follow that approach.
I think the “reach” problem could easily be worked around at initial design time, by simply allowing the carriage to travel beyond the bed. Allowing e.g. a 5-10cm over-reach would allow for things like an upward looking camera, or to reach a part feeder/tray.