BigTreeTech BTT SKR Pico V1.0 is a 3D printer controller board based on Raspberry Pi RP2040 MCU, compatible with Raspberry Pi Linux SBC’s, and specially designed for the compact Voron 0 3D printer, but also working with other models.
The board comes with four TMC2209 motor drivers covered by a heatsink for cooling, as well as interfaces for temperature sensors, and a USB Type-C port to connect to the host computer, usually a Raspberry Pi board running Linux.
BTT SKR Pico V1.0 3D printer board specifications:
- MCU – Raspberry Pi RP2040 dual-core Cortex M0+ microcontroller at up to 133 MHz with 264 kB of embedded SRAM
- Storage – TBD
- Motor drivers – Up to 4x TMC2209 drivers for X, Y, Z1, Z2, and E interfaces
- Temperature sensor interfaces – TH0, THB 2-way 100K NTC RTD sensors
- Host interface – USB Type-C port
- Misc – Built-in heatsink (Note: fan cooling is required/advised for motors drawing more than 0.8A)
- Power Input – 12V or 24V DC + fuse
- Dimensions – 85 x 56 mm (4-layer PCB)
The board is optionally offered as an “Armored” version with the protective top cover and can be mounted to a Raspberry Pi 4 or Raspberry Pi Zero 2 W or earlier models in order to run Klipper or Octoprint. It’s been designed as a more compact replacement for the earlier BTT SKR Octopus board.
The Voron 0 (now Voron 0.1) is an open-source hardware 3D printer that you can build yourself, or purchase for about $400 on Aliexpress or other websites.
BigTreeTech BTT SKR Pico V1.0 is available for $35.68 USD on BIQU website, while the now out-of-stock Armored version is usually sold for $39.98 USD.
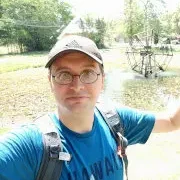
Jean-Luc started CNX Software in 2010 as a part-time endeavor, before quitting his job as a software engineering manager, and starting to write daily news, and reviews full time later in 2011.
Support CNX Software! Donate via cryptocurrencies, become a Patron on Patreon, or purchase goods on Amazon or Aliexpress