The SGET (Standardization Group for Embedded Technologies) non-profit organization ratified another system-on-module standard last November, with the “Open Standard Module” (OSM) standard that instead of relying on edge or board-to-board connectors is meant to be soldered on the carrier board as a solder-on module LGA package.
F&S Elektronik has unveiled one of the first SGET OSM compliant SoM with “FS 8MM OSM-SF” equipped with an NXP i.MX 8M Mini processor, up to 8GB DDR4, 32GB eMMC flash or 512MB NAND flash on a 30x30mm “Size-S OSM” form factor.
FS 8MM OSM-SF system-on-module
- SoC – NXP i.MX 8M Mini single, dual, or quad-core Arm Cortex-53 processor @ 1.8 GHz with real-time Cortex-M4 core @ 400 MHz, Vivante 2D & 3D GPU, 1080p60 H.265, VP9, H.264, VP8 video decoder
- System Memory – Up to 8GB LPDDR4
- Storage – Up to max. 512MB SLC NAND flash or up to 32GB eMMC flash
- 332 balls contact grid with
- Storage – 2x SD card interfaces
- Display
- 1x 4-lane MIPI DSI interface
- Analog resistive and PCAP Touch ext. via I2C
- Camera I/F – MIPI CSI interface
- Networking – Ggiabit Ethernet
- USB – 1x host, 1x OTG 2.0
- Serial – 1x CAN, 4x UART
- 4x I2C, 2x SPI, up to 32 digital I/Os, PWM
- Audio – I2S, ESAI, SAI, SSI, SPDIF
- RTC
- Supply Voltage – 5V DC/±5%
- Power Consumption – 3W typ.
- Dimensions – 30x30mm (Size-S “Small” OSM)
- Weight – 7 grams
- Temperature Range – 0°C – +70°C; optional: opt. -20°C – +85°C
The company provides supports for Buildroot & Yocto to build a custom Linux image running on the Cortex-A53 core(s) and FreeRTOS for the Cortex-M4 microcontroller. The module will be available until 2029.
Open Standard Module (OSM)
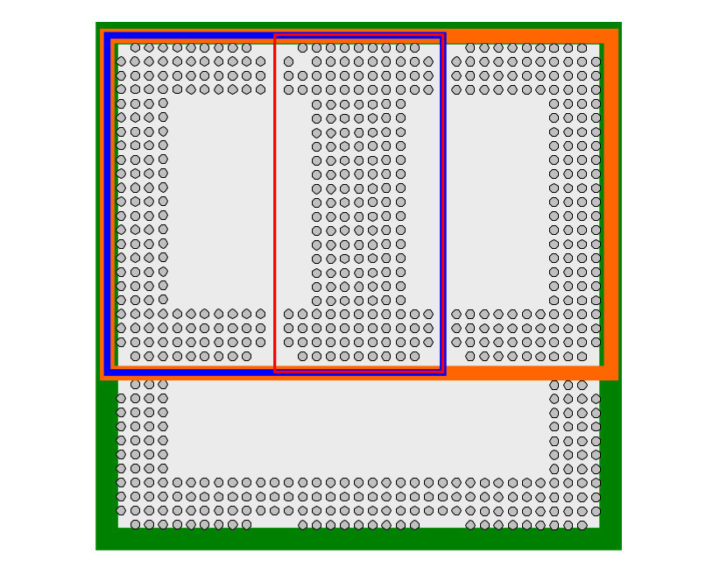
While F&S Elektronik currently only announced a”Size-S” OSM module, there are four different sizes defined in the specification.
- Size-0 – “Zero”: 30 mm x 15 mm with 188 contacts (see red outlines above)
- Size-S – “Small”: 30 mm x 30 mm with 332 contacts (see blue outlines)
- Size-M – “Medium”: 30 mm x 45 mm with 476 contacts (see orange outlines)
- Size-L – “Large”: 45 mm x 45 mm with 662 contacts (see green outlines)
The document also details all pins with only a few being mandatory (e.g. UART, RTC), and most being simply recommended or optional.
While I believe it’s the first industry-wide system-on-module standard that is meant to be soldered, some companies introduced their own private standard in the past with for example TechNexion XORE, and we’ve seen many application processor modules with castellated holes or pads.
Only limited details are available on F&S Elektronik’s product page at this time, but the company will host a webinar on May 6th with plans to discuss the advantages and challenges of using a solder-on-module following the OSM standard, and how to start development.
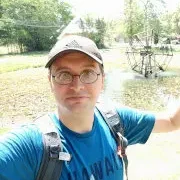
Jean-Luc started CNX Software in 2010 as a part-time endeavor, before quitting his job as a software engineering manager, and starting to write daily news, and reviews full time later in 2011.
Support CNX Software! Donate via cryptocurrencies, become a Patron on Patreon, or purchase goods on Amazon or Aliexpress