Hey Karl here. I am going to be sharing my experience with the xTool D1 Pro 20W. It is a 20W laser cutter/engraver with a 340x390mm working area. It has been heavily reviewed and I will comment on a few points I have not seen spoken about. I join a lot of Facebook groups for these reviews to get real-world feedback and ideas to write about. With nearly all forms of digital fabrication, I regularly read about misconceptions and frustration that stem from unknowingly purchasing a machine that requires a substantial amount of time and patience to learn.
For this review, I kept a daily log and will summarize the time it took me to complete one project. I did get sidetracked on a few aspects and will take that time out. I am excited to share the results of the laser power testing I have been doing.
Logs will be short and to the point. I only did some light editing. This is not to scare anyone off. I want to inform and encourage. I really like the challenge and learning new techniques and processes. It entertains me immensely. There is also a short list of items nearly everyone should get in my opinion and should be taken into account when budgeting. All the extra stuff adds up quickly.
I have already invested quite a bit of time in various different CNC machines and would not consider myself a novice.
Before I begin I have to prepare my space for this project. I am reviewing this in my office/workshop in the winter and that presents some challenges. Lasers produce particulates and they need to be removed from indoor environments. I purchased a soft enclosure with exhaust and will share that experience.
For my project, I made a gift for my wife. I had design elements that I wanted to incorporate but not a clear picture. The elements that I wanted to incorporate were
Leaning towards a boxCustom Mandala ArtCut thin metal and artificially rust/weather itLaser cut 45deg cornersEngrave artStretch goal to engrave shadingMostly plywood construction
That all went out the window mostly.
I anticipated 3 weeks to fully set up and complete this project. I have up to about 3 hours a night after the kids go to bed before I am ready to hang up my hat.
Summary
Overall I like it. Very strong 4-diode laser module. I am amazed that this is even possible. I would be really interested to see how this is assembled and I would guess they are assembled by hand.
Like
- Fully contained. No moving parts outside the boundaries to snag on.
- Offline mode. Not documented well but is a definite plus.
Dislike
- Mesh loom for wire management. Easy to snag
- Focusing is rudimentary
- Firmware is locked down and uneditable.
Unknown
- Metal on metal motion system. I am not sure if this is a concern or not. Last 2 pictures below show metal rollers on round metal rails. I would like to hear opinions on this. If you have any experience with this please share.
Price: $1,103.99 (Promotional price). Regular price listed on the website: $1,399.99.
xTool D1 Pro 20W assembly pictures
The longest part of the assembly for me was getting the tiny cables connected.
xTool D1 Pro 20W review logs
- 1/26 9:21 11:20 ET Setup/Test
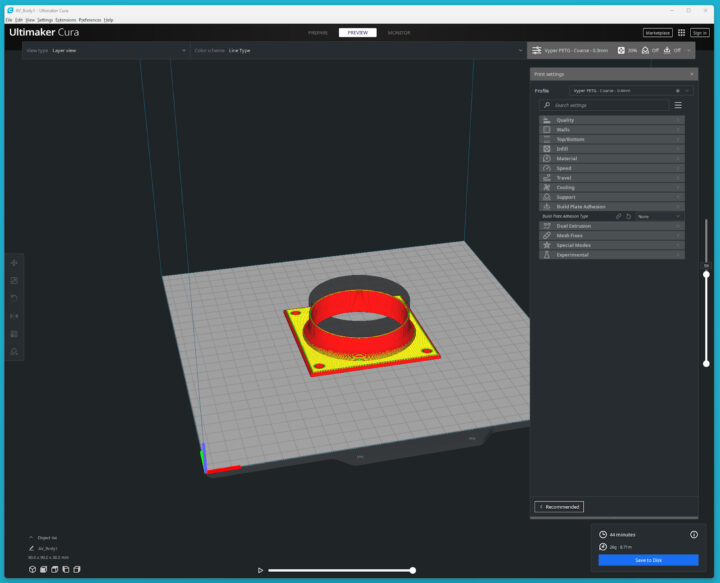
Initial setup. Constructed enclosure. I determined I cannot do this on my 24” deep desk. Using my CNC bed, the hose comes out of the back and hangs off the desk. The first part of the exhaust is finished. Designed and printed. After printing, I realized I missed some geometry and will have to print another piece to complete it. I updated Lightburn and renewed my license: $30. The Lightburn profile was downloaded from the support forum and installed it. Lightburn doesn’t recognize it automatically. What took the longest was updating the firmware. I used the standalone tool. The instructions weren’t good. xTool Creative space ended up installing an even newer version not available when downloading the standalone tool. The cables I was complaining about when assembling were not seated all the way. Limit switches were not connected. Fully seating fixed the limit switch issue.
- 1/29 9:35 10:51 Setup
I took the weekend off. But I printed and installed 2 things: legs and some wedges. I’ll add about 15 minutes. The goal today is to first power tests with a DIY meter and finish the exhaust. I talked with my Dad about the project. I am concerned that a single fan won’t be enough. He suggested adding additional 120mm fans. I may try that if that one is not enough.
Mistakes were made. Not bad, but not very conclusive power tests so far. Had trouble getting the timing right for the power test. 17.88W…..but I had 2 failed tests and the aluminum is already heated. Going to move over to fusion and finish the fan. If cooled off, I will retest it at the end of the night.
Doing some research for combining fans before. This looks like it will be a fun test. I tested the 80mm fan that came with the enclosure and it moves some air. I think static pressure will be key. It will have to pull in the air in from cracks. I did a little test inside and it was able to suck in the smoke. Amazon has some fans that look promising just a few clicks away if the included one does not work. I also “overclocked” the fan to 19V for a few seconds and then it was moving some air. I found some bitminer replacement fans touting 5000-6000 rpm. The price is right and I am hoping that I don’t have to go all out and get a $100 exhaust fan. An exhaust vent is looking more and more like a required maker accessory. I had to stop a resin printer review. I couldn’t handle the fumes. I probably could press through but I was getting headaches and didn’t want to change it. Anyway….a hood would have been great for that. It would be nice for printing too. I am thinking of an industrial hood with a removable curtain and a variable-speed fan.
2nd test mostly ambient: 18.37W and another at 18.37W an hour or so later
- 1/30 9:17 11:45 Meter
I had an epiphany I believe regarding a DIY laser power meter. It has been a project I have been toying with for a while now. All my testing thus far came back resulting in power measurements pretty close to the rated values of the laser. I have seen very few reviewers actually measure laser power so I didn’t have anything to compare to. These lasers and software have safety features in place that stop the laser from just firing while sitting still. So what I have been doing is setting up a laser job to burn a 1mm circle @ 1mm/s and a number of passes to meet the time. I had found that LightBurn has been pretty good at approximations and didn’t really question it. The software knows all the motion parameters. This is my fatal mistake, I believe. On the xTool, my times were way off and I ran a test run and used a stopwatch to get the time. This is not accurate enough in hindsight. One second makes a huge difference in calculations. So what I am going to do is run the 1mm gcode and record it. Bring into video editing software and measure in software.
This is not good. Two tests are exactly 11 seconds….Two are 11.5 seconds.
Hmmm… 18.37W again… at least it is consistent. It must have been pretty close. We can’t read too much into this. I have been changing other variables.
I remembered I did some tweaking to the software so I removed the tweaks. Now I am getting 15-16W. I need to let it fully cool and try again.
No real progress tonight. I will revisit power later. There are safety mechanisms in place to stop the laser from firing while not moving.
- 1/31 9:25 11:33 Meter
I believe the DS18B20 temperature sensor I am using is causing the issue. It has a stainless steel shell. Going to check the math to see if I can fire the laser directly at the shell. OK, the math is not working out. It would raise the temperature too much. I’m going to find a different probe.
I spent a few minutes looking and decided on the same sensor but with a different package. It makes it easier to swap out. Also going to change an unused 3D printer heater block. The sensor should fit where the heat cartridge goes nicely. The math works out nicely and should be able to measure up to 80 Watts with a 5-second burst. I will look for a better piece of aluminum.
Next, finish the exhaust. This was way easier than I thought it was going to be to finish. The design is complete and the print started. I’m calling it quits for the night. I should have done this last night. Nearly ready to cut. I also ordered the new temp sensor that will be here on Thursday.
I wanted to find a more reliable repeatable way to test fire. I ended up having to monitor the serial port to find the commands below. It took way longer than expected. It took a little bit of efforts to find the correct formatting.
1 2 3 4 5 6 7 |
mode COM4 BAUD=230400 PARITY=N DATA=8 echo M3 > COM4 echo G1 F100 S1000 > COM4 timeout /t 10 echo S0 G0 > COM4 echo M5 > COM4 pause |
I got the exhaust running. Pitiful. Ordered a 6” duct fan on eBay for $67.
- 2/1 9:09 9:50 Setup/Test
I won’t be able to make much progress tonight. I received a notification that FedEx should deliver the fan on 2/6. I need to mock up the setup to get my exhaust pipe length. OK, I need to regroup. My CNC bed is not big enough. I will have to use my benchtop. It is just barely big enough. I’m thinking I will cut a hole in the top of the exhaust chamber depending on how big the fan is installed directly in the top. The window is within 30cm. I might be able to print something instead of purchasing a pipe.
I saw that xTool came out with a 40W diode version…This video shows cutting a 2×4 pine board as an intro. That is pretty impressive. It is combining 8 diodes I believe. Very close to CO2 territory. Short night tonight.
- 2/2 9:04 11:05 Meter
I got everything built and it is reacting much better. I need to rent a nice laser meter. I am using the fan that came with the exhaust kit to cool it back down. The block is not insulated. The temp sensor is wedged in with a thermal compound. The next step is to glue it in place. I have some cheap thermal epoxy I will test next. That will help determine how repeatable this is.
Done several tests
- 20.34W after a little bit of manipulation in the code.
- 20.85W it was a little closer to room temp this time.
- 18.8W outliner. I did not have the surface perpendicular.
- 20.53W
- 50% Power Approx 10 deg – 10.36W
- 25% Power -4.48W
My initial reaction is that for a lower-power test, the block needs to be even smaller. The temp only rises by 3 degress celsius.
I will probably tweak the batch file to accept length and power and com port. Right now, I just created a couple of batch files.
- 2/4 10:10 12:07 – Power meter software
Tonight was strictly software for the power meter. Repeatability is the name of the game. During testing, I found that the power calculated only worked reliably if the aluminum was starting from room temperature. I performed several measurements without being at room temperature and used a function equation finder website to find the function. I incorporated it into the code and calculated the offset. I was not expecting it to be linear. But after thinking about it….the rate of heat loss should be linear. I used my approximate room temperature of 23 deg. The next step is to see if I need real-time temperature measurements and incorporate them into the equation and test existing code in a cooler and warmer room. Right now, I am really happy. This is all assuming that this laser is outputting 20W. Throwing out the 1 highest and 1 lowest measurements resulted in a delta of 1.25 Watts. If I have to take into account the real temperature I am going to be in trouble. Going to leave my heat off tonight in my office and see how it performs in the morning. I might have to get some help with the math.
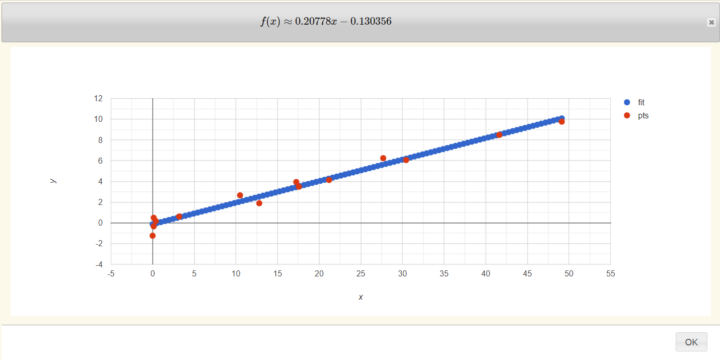
I try not to work on the weekends, but it was a lazy weekend. Super ecstatic about the results. Results are even tighter this round with an approximate .5W. The ambient temperature doesn’t seem to have an effect. I tested around 16C and got the results as expected. But I did find that time affects the results. Testing below 5W did not give consistent results. The rise in temperature is only a few degrees so I tested increasing the laser on time to 20 seconds and adjusted the variable. But again not what I was expecting. I am not sure if I can manipulate the existing formula. Or if I have to calculate for each time duration. Enough on this long-term side project. But if you read this xTool. It would be awesome if I could test out your 40W laser with this side project.
- 2/6 9:15 10:54 Project
I was expecting the inline exhaust tonight but looks like Fedex is wrong again with their estimation again. It almost always takes an additional day. I finally sat down with my wife and was explaining what I was doing to get her input.
Leaning towards a boxCustom Mandala ArtCut thin metal and artificially rust/weather itLaser cut 45deg cornersEngraveStretch goal to engrave shadingMostly plywood construction
After showing her some examples she liked the idea of just Mandala wall art so tonight is starting on the design. I am not sure exactly what software I will use. I am suspecting a combination of Inkscape and Fusion 360 and full rendering in Fusion. I could just buy a premade design but I want to create a custom one. I would like to incorporate a beachy theme. She loves the beach.
OK, not much progress tonight. I might have bitten off more than I can chew when it comes to creating this from scratch. I found a Mandala Art generator. I played around with it in the last few minutes. It will be simple if I can make it work.
- 2/7/ 9:05 10:30 Project
I studied some pictures and am going to try a different strategy. I was trying to go from the back to the front…I am going to try the opposite direction tonight.
I received a new inline fan today. It is not the best quality and has a slight shake at full speed. Much quieter and seems to move a bunch of air even with an obstruction. It has some weight to it. I was going to cut a circle in the top of the enclosure and connect it directly but it weighs too much.
I am feeling defeated. I might have to just find and purchase. I don’t want to spend much more time in this phase. Little to no progress.
- 2/8 9:21 11:15 Setup/Project
I finally found a good guide so I could make a passable 3D mandala. I did a test and for a first try, I liked it. Also if you read my last review….I am now back to bare metal with the 3900X and letting it stretch its legs. This is when I rendered it in Fusion. It gives a good idea of the final outcome.
I also designed and printed a 6” flange for the enclosure. I am going to super glue to the enclosure and cut a vent hole. Vent pipe is problematic. It doesn’t matter where I look….I see negative reviews saying it is extremely flimsy. I am going to go to the hardware store and will probably go rigid. It is such a short run I think I can do it with just a few pieces of rigid duct.
- 2/9 9:29 10:45 Project
I feel good about the process of creating. Just need to find a better application. Fusion did not like all the geometry and is not optimized for all the mirroring and circular patterns. It was nice to be able to update 1 pattern and all the rest followed but Fusion is poorly optimized.
So I tried a different method of creating the pattern on this website and tested it out. All went well. A couple more tests and then get my wife’s input on the different styles. I will see what she thinks and make a decision to purchase or move forward with the custom design. I like the idea of custom designs but dang it takes so much time…..She is in bed already and will see what she thinks tomorrow and make a decision. I am only going to use the generator as a reference and trace. I had some issues with the vectors not being closed. I also tested out variables. I can change offsets en masse this way.
- 2/13 9:04 10:11 Setup/Test
Not much action tonight. I forgot to pick up super glue. I installed some command strip hooks to hang the blower. Printing off a transition from 6” pipe to square hole. It took a few minutes to model this. I tried vase mode, hoping the .6 nozzle would be rigid enough but it wasn’t. Reprinting again with 3mm thick walls. I got feedback from my wife over paid designs vs custom….I will find one to purchase. I liked the thought of a custom one but don’t really want to put all the time in. I’m going to sit down with her tomorrow and get one picked. If everything goes well I should be burning tomorrow.
- 2/14 9:16 10:00 Setup/Test
I glued the flange to the enclosure. Let it dry overnight. I designed one last piece to transition to the outside. I just created an extra piece in Fusion and I will glue it to the existing one instead of printing a whole new piece. I really don’t like this final setup but will move forward to get this project done. I should be cutting tomorrow.
- 2/15 9:19 11:15 Setup/Test
I really wanted to start laser cutting/engraving tonight so I spent a few minutes gluing and securing the final parts for the exhaust. While I was getting glue, I found some wood coasters in the arts and crafts section of the Dollar General store in my town. They look to be made of balsa. I want to try a technique I have been wanting to try for a long time and that is to etch a shape then go back and fill it n with UV resin then sand flat. My wife hasn’t finalized on her design so picking up a few side projects.
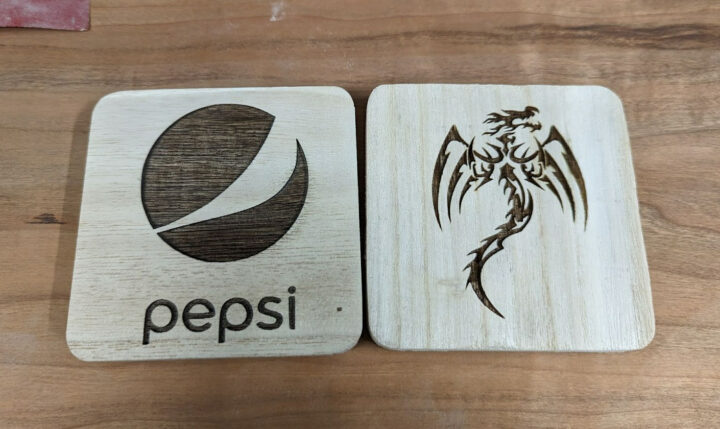
I couldn’t be happier about the first test. I tried with and without a mask to see how valuable a mask was. It looks like I am going to be ordering some wide masking tape. Tomorrow is the real experiment using UV resin. This is a good start. Nice and deep engravings.
I still have some wood-burning smell. Not a perfect exhaust solution. I will keep working on this.
- 2/16 9:10 11:00 Setup/Test
I took 5 minutes today to put a clear coat on the Pepsi coaster. Wood is really porous. Clearcoat is to serve 2 purposes. Seal the wood so the resin doesn’t seep into the wood, and protect the wood when sanding the black resin and grinding into the wood.
The resin is set. I don’t feel like my UV light is strong enough to penetrate all the way. I’m going to put it outside to fully cure and sand. It looks promising.
I tried steel business cards. It took several tries but it’s a fun little project
Steel Business cards 200 mm/s 20% power .15 Darkened image to show better Jarvis 4.5min in the right light it looks stunning
I also did a small wooden coaster. Wood 150mm/s 85 1 passes 4.5 min
- 2/20 9:05 10:28 Setup/Test
I really don’t like the focus adjustment. I think I have a simple way to assist. Also going to test out focus. I found my focus jig from a couple of lasers ago.
Just finished for the night. I required about 3 cents worth of plastic and now I have a marginal improvement over stock. Fine for now but I want to fix this properly some time later.
I also tried a focus jig and it was inconclusive. The Focus arm seems fine.
- 2/21 9:00 10:30 Setup/Test
I didn’t like the first revision. I did a quick revision of the Z lifter. Much better and more sturdy. It took a few minutes to model and print. 9:45 now. I found 20 or so files and cornered my wife to pick one. I think I am going to do multiple things. There is one compass that I saw that looks awesome.
More stuff was delivered today. 12” masking tape
- 2/22 9:04 10:20 Project
First cuts tonight… lots to experiment with. I found kerf offset to friction fit parts. It is about half of the beam width of .07 to get spot-on friction fit and dimensionally accurate parts.
I tested some cuts. My wife finalized the design from Etsy. Now she has to choose the colors.
I found the parts really accurate and get super detailed.
- 2/27 9:22 11:20 Project
Starting cuts. I printed off some hold-downs for the honeycomb that friction fit.
I forgot to put on masking tape for the first cuts, and ran into some learning pains that slowed things down tonight. 4 layers cut. It looks fantastic to me.
I’m getting too many spots that aren’t cutting through and it’s taking too long to clean up. Slowed down 1mm/s running 90% 7mm /s
Need to improve ventilation, as I’m getting some smoke smell in the workshop. 15-minute cuts. The last cut is much better after slowing down…going to lower the laser a mm or so to focus the laser just below the surface. I might be able to get that mm/s back. I added a couple of minutes to the cut. This is going to take several nights to finish.
- 2/28 9:20 11:22 Project
At it again tonight with 5 more cuts.
- 3/1 9:12 10:30 Project
Final 5 layers tonight. I had one snag, as I forgot to put the focus arm back up and snagged and ruined the cut. Almost ready to glue, seeing if she wants an accent color on one layer. Much easier tonight.
- 3/2 9:14 9:45 Setup/Testing – Off-line mode
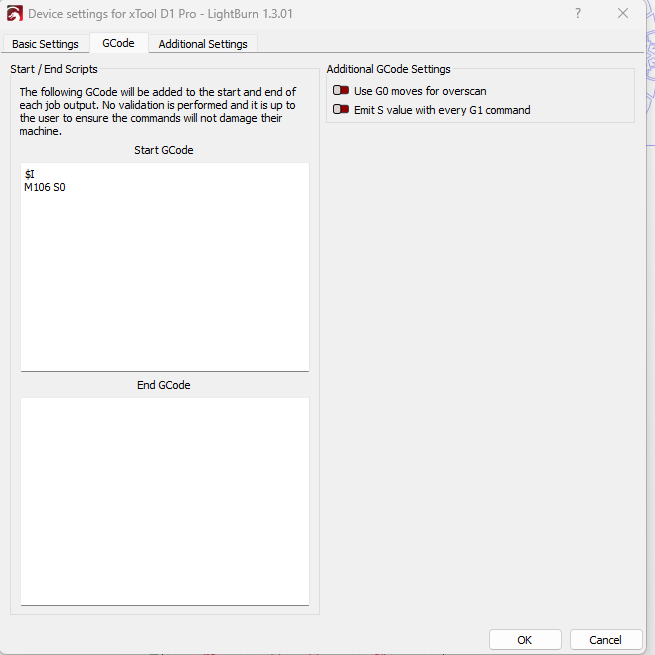
Just a few minutes of testing tonight. Last night before going to bed I asked a question to xTool in the forum about offline laser cutting/engraving. It is advertised but I could not find documented information on how to use it. This is really important to me. I have found it problematic in Windows to stream gcode to any CNC machine. Linux has been fine. Long story short, the gcode must have $I as the first command, and the file is named tmp.gcode on the SD card. I just added $I to Lightburn start gcode under Edit > Device Settings > Gcode > Start Gcode. The xTool D1 Pro 20W machine is not automatically configured by probing the machine like other laser engravers. I would suggest xTool to add this to the profile that they provide for importing the settings in Lightburn.
This will finish up and I will summarize my experience.
Time and Total Cost Summary
33.75 hours in total and that does not include writing nor some light research reading.
- 11.5 hours setup and testing
- 10 hours working on the power meter
- 12.25 hours on the project.
740x700x400mm Enclosure | $63.00 |
---|---|
Inline Fan | $67.00 |
6" Duct (Lowes) | $32.00 |
12" Masking tape | $41.00 |
Honeycomb Bed | $50.00 |
Air Assist | $26.00 |
Total | $279.00 |
Final thoughts about the xTool D1 Pro 20W
In summary, be prepared to fork over time and money. In my opinion, nearly everyone should use an enclosure with an exhaust system. Safety will be improved, then there are all the other things that improve the quality of life listed above.
Admittedly I am not even finished with the project completely so will have some more time for gluing up and framing. We got a cold snap and I want to finish outside which I should be able to do this week hopefully.
These types of projects and tools are right up my alley. I like the challenge and have the time to invest. The xTool D1 Pro 20W is an investment but you really can make some awesome projects with it. If you are interested in picking one up you can pick it up at their official website currently for $1,103.99 plus an extra $50 discount for St Patrick’s Day, or Amazon for $1,119. Both are on sale right now.
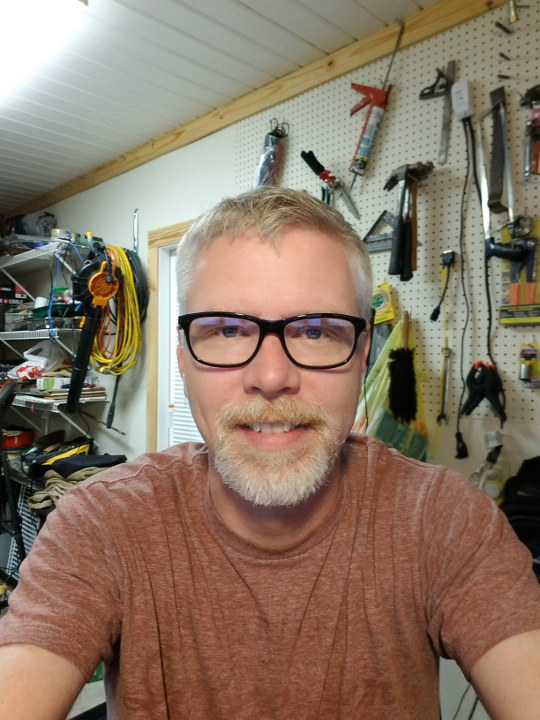
Karl is a technology enthusiast that contributes reviews of TV boxes, 3D printers, and other gadgets for makers.
Support CNX Software! Donate via cryptocurrencies, become a Patron on Patreon, or purchase goods on Amazon or Aliexpress