Hey Karl here. Today we are going to look at something a little different. I am writing about my experiences with building Genmitsu 3018 CNC router upgraded version provided by Sainsmart for this review. While waiting on the unit to arrive I did some research and found that there are several different versions on the market labeled CNC xxxx. The xxxx represent the build volume in the x and y. So the one I was sent has a 300x180mm build volume. The 3018 is called upgraded because the new mounting for the X and Y rods and lead screws.
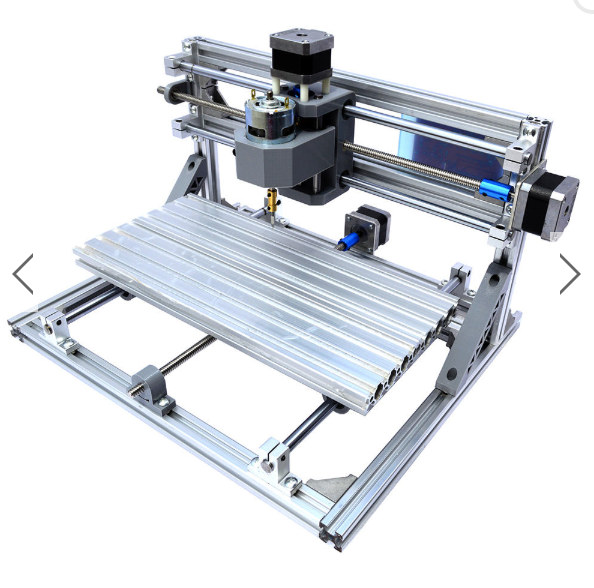
On the previous version these had to be mounted and manually aligned which from what I read can be a pain.
Building Genmitsu CNC 3018-PRO CNC Router
The build went very well. The 3018 user manual was mostly pictures but they called out anything that might be questionable. I had been talking about the CNC/engraver with my kids and they were excited to help build one evening after school. It took us about 1.5 hours to build and I was only able to keep their attention for about half the time. We put it together on our carport on a rug… my back wishes it was at the workbench. I normally put together in my shop but wanted them involved. I am a little above average height and my workbench is at my standing height in my shop so opted for the floor. I had three issues were I had to redo but all were my fault and easy to fix. I just didn’t pay attention to detail. I bet I could easily put it together by myself in about an hour under better circumstances. I did record the build but found it not very interesting and useful to share.
One thing to note. I did find a ball bearing in the box but can’t confirm it was from this kit. Everything seems tight and no slop in movement.
First Etches with CNC 3018-PRO
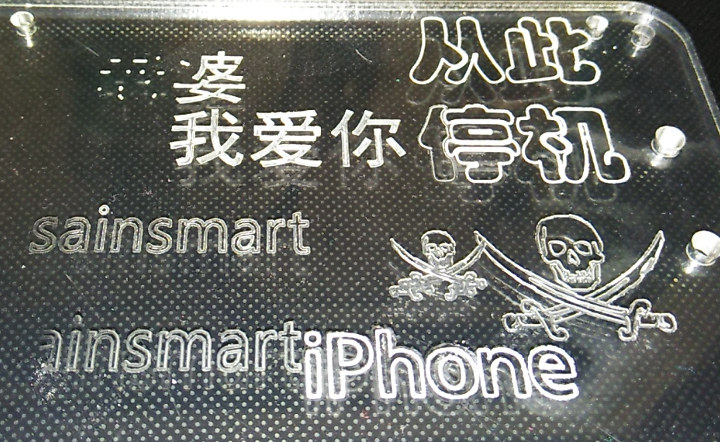
The kit came with a mini CD but I skipped using it and downloaded the documents and software from Sainsmart wiki. It has a digital copy of the instructions as well as some windows software and drivers and some gcode for testing. I connected the printer to my PC… I didn’t have to use the provided drivers…then loaded the example gcode. Before starting I positioned the bit at the bottom left hand corner with the tip barely touching. I set X, Y, and Z to 0 home position in the software. Then hit run. I etched the Sainsmart logo on a piece of acrylic with very little effort. My first pass wasn’t perfect, the s and a only partially showed. I am not sure if it is uneven bed or the acrylic was uneven. I started again and it was fine. While using the CNC router, I realized if that happens again I can just go down to 0 height then go 0.1mm lower and zero only the Z and start again if I have only partially etched something. I etched the rest of the examples with very little effort. I am doing just simple etches right now to get a feel for speeds and feeds. I think I have been very conservative. 600mm/min feed and 120mm/min plunge at .5mm depth per pass.
Windows and USB
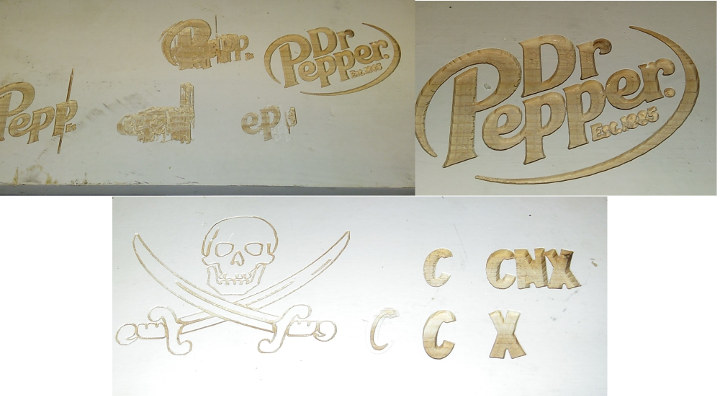
I really don’t think that a Windows machine is best suited to send gcode. I was using an old laptop that had Windows 10 on it. I had some issues with timing out when the screen turning off. The spindle would just stop until I moved the trackpad. I am sure there is a windows setting other then don’t turn off the screen while plugged in but wanted to go straight to a permanent solution. On one instance my battery drained and surprisingly when I plugged it back into mains power the etch resumed like nothing happened. I also had some issues with the provided cable. After a long period of time my laptop would loose connection. I have a tiny 3” mini USB cable that I used without issue. But It is really hard to use a cable like this with a bulky laptop. I found a web based app that I installed on a Raspberry Pi called CNCjs that is working pretty well for me. I did try the CNC plugin for Octoprint but without success.
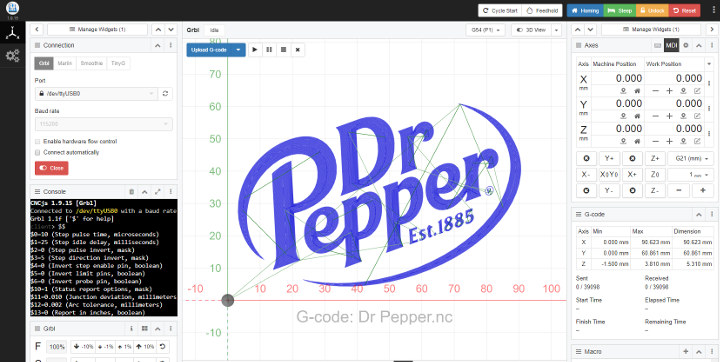
1 gripe
As you can see above I had some issues with the Dr Pepper logo. All of them were due to these grub screws coming out. I wish some threadlock was included. No matter how hard I tightened the grub screws they came loose. I couldn’t get enough torque on them. I had some m4 that I put in temporarily until I get some. I would leave but it reduces the build volume.
Random things
There is a very simple board provided. I did not have to adjust the stepper drivers so far. No missed steps but again I have been conservative. There is also a connector for a laser which could be interesting to explore. Grbl 1.1f is pre-loaded. I started with an older Raspberry PI to host CNCjs but 3+ is superior as far as speed goes. I recently purchased an infrared thermometer and so far everything is running cool, and nothing was over 40c.
Testing and Wrap Up
So this is part 1 and initial testing and build. I want to test milling some pcb’s and have some blank pcb’s on the way from Amazon as well as some square end mills. I will test some hardwood lumber as well. I hope to get some carbon fiber sheets and finally test the dimensional accuracy. I might try an engraving on metal but I really don’t think the 3018 is up for any cutting. I have barely touched the surface and only done simple cuts. I still need to learn Fusion 360 cam. I used easel to generate the custom gcode. I tried a simple toolpath in fusion 360, but need to spend more time on it. There is a lot to it and need more time to master. If you have any tests you want to see leave a comment below or a project idea. I will record some cuts and fusion work.
Big thank you to Sainsmart for providing the 3018 to test and review, and to Gearbest for sending the Raspberry Pi 3B.
Continue reading “Genmitsu CNC Router Review – Part 1.5: Laser Attachment“
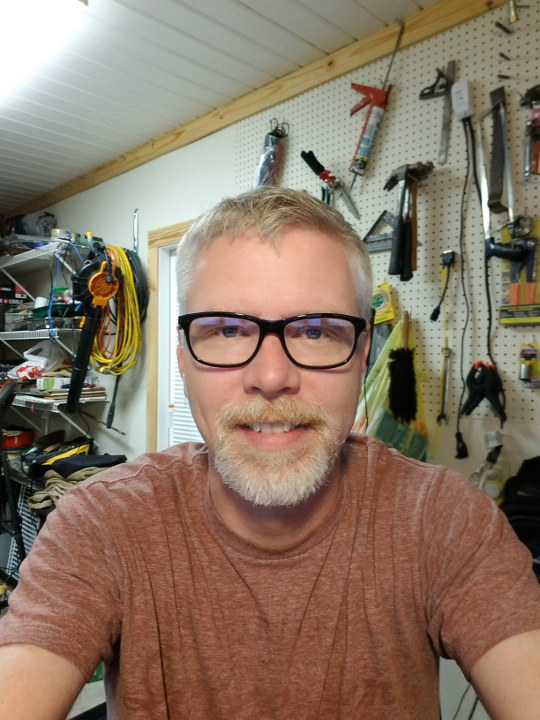
Karl is a technology enthusiast that contributes reviews of TV boxes, 3D printers, and other gadgets for makers.
Support CNX Software! Donate via cryptocurrencies, become a Patron on Patreon, or purchase goods on Amazon or Aliexpress